The thermal performance tests failed today. The case temperature went up to 85ºC after just 30 minutes. The die temperature was 105ºC. No good.
A re-design was needed. I was trying to avoid using bigger heatsinks as they increase the protrusion of the lamp. Also they are expensive. I do however have some good heatsinks from a previous project. Integrating these into the design meant almost an entire rework of all the mechanical parts. I had to turn the cases over because the surface that I originally had the LED mounted to now has more holes in it than a second hand dart board. Some of the existing holes would interfere with the new design.
So these are the heatsinks I am now using with the LED, once again, glued on with Arctic Silver epoxy.
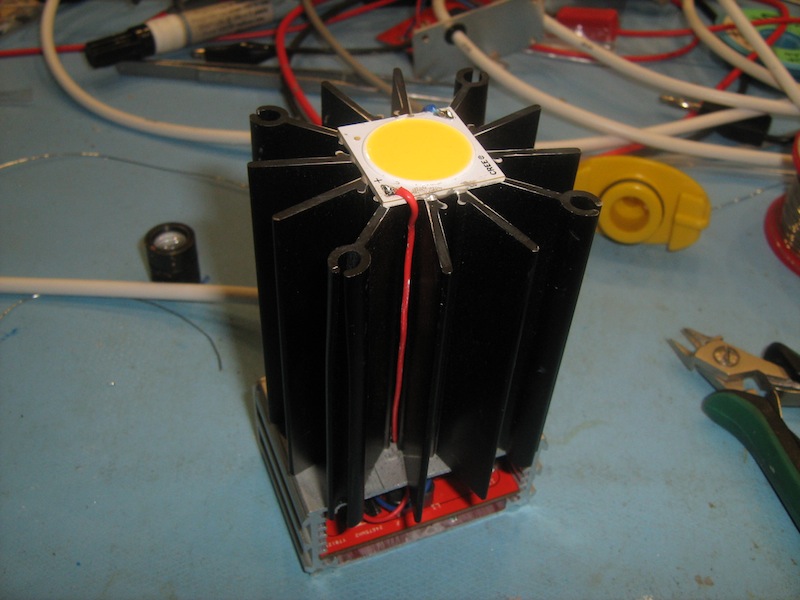
I then enlarged the hole in the centre of the dog bowl to allow for better flow of convection currents. Besides, the mounting holes are now on a much larger diameter.
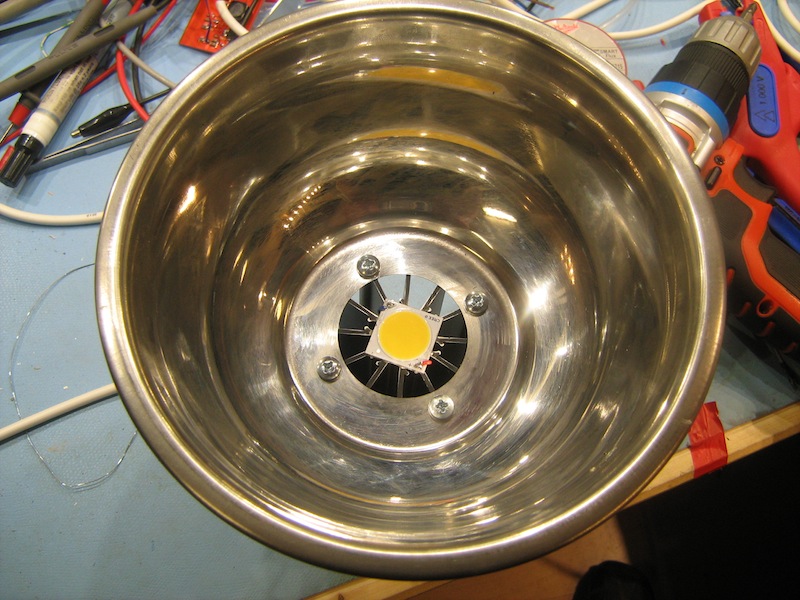
Now the thermal performance is much improved. I left the lamp on for two hours and the heatsink temperature rose to 50ºC and the die reached about 85ºC. That die temperature is actually what these LED's are binned at so that was a nice coincidence. The glue is performing well now that it is bonded to a better performing heatsink.
Here are two of the lamps in position. Now I am getting 2500 lux on my worktops for less energy as opposed to the 250 lux I was getting from the fluorescent lamp. Granted, the fluorescent lamp was not in the same position, but directly below the fluorescent lamp at the same height I get 450 lux.
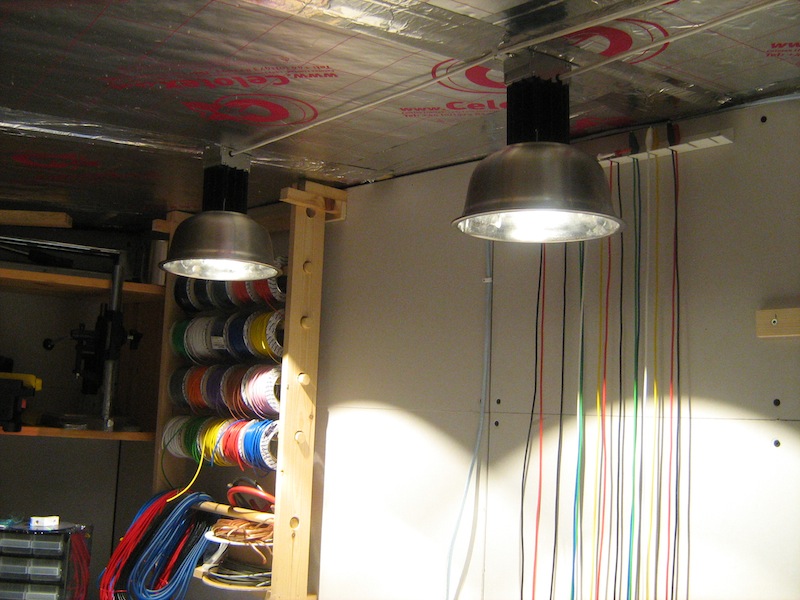
Shadows are a minor problem, about the same as you'd get from a CFL. I plan to reduce the shadows with some diffuser material.